Industrial Product Design Strategies for High-Performance Products
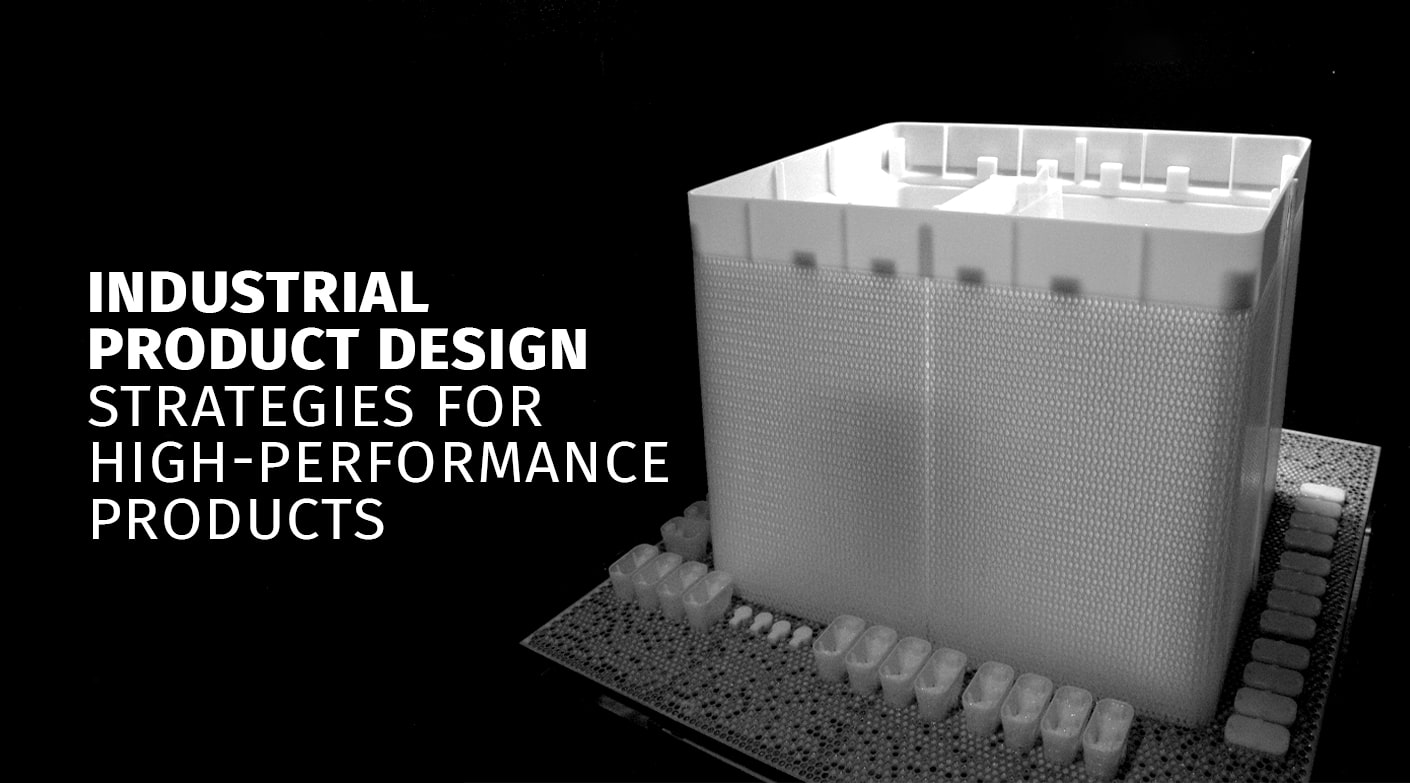
When Los Angeles-based Czinger manufactured the 21C hypercar, it broke multiple speed records, an international F1 circuit. The high-performance sports car was an innovation driven by 3D printing and AI and exemplified what the right industrial product design strategy could do for the world of automotive manufacturing. In healthcare, a new value-based patient care was made possible by scientists at UWE Bristol, where the first 3D-printed food specifically was designed for dysphagia patients.
This innovation is set to solve the challenges for patients with swallowing difficulties and is set to be a pathbreaker.
These examples demonstrate the impact and potential a well-thought-out industrial product design strategy can have on high-performance products across industries.
In this, we touch on the subject of high-performance products, and some of the effective design strategies that can lead to better quality, durability, and performance.
Top 6 Industrial Design Strategies for High-Performance Products
1. Design for Manufacturability (DFM)
What if you could avoid costly redesigns and production delays by addressing potential manufacturing challenges right at the design stage? That’s what design for Manufacturability (DFM) is all about.
According to McKinsey, adopting Industry 4.0 solutions, which includes DFM practices, has been shown to improve labor productivity from 15% to 30% across various sectors.
Cubein’s turnkey manufacturing services are based on DFM and are aimed at helping organizations prevent costly redesigns and production delays by addressing potential manufacturing constraints early.
DFM is one of the key industrial product design strategies that simplifies geometries and reduces material usage while maintaining strength, adding appropriate draft angles to facilitate part ejection, and avoiding complex undercuts.
2. Utilize Rapid Prototyping for Iterative Improvement
If rapid prototyping of high-quality products is your ultimate aim then 3D printing is the way forward as it allows quick iteration of design concepts. Rapid prototyping for iterative improvements is one of the leading industrial product design strategies that has the potential to reduce the design-to-production timeline from months to weeks and can help reduce the cost for prototypes by approx. 2-10 times.
3D printing or additive manufacturing is an agile approach that helps refine products faster, helps to quickly identify design flaws, and makes improvements. Now who wouldn’t want to test multiple variations without incurring significant expenses?
Rapid prototyping with 3D printing helps in improved risk management where any potential risks are easily detected and mitigated before moving to large-scale production.
Stat Insight: A study conducted by Wohlers Associates revealed that 68% of manufacturers use 3D printing for prototyping, significantly reducing design cycle times by up to 75%.
3. Material Selection for Performance Optimization
What if the Tesla Model 3 was 3D printed using foam instead of durable, high-performance materials? It might not exactly be the high-performance ride you’d expect when you’re looking for speed, durability, and safety on the road! This is why choosing the right material is vital for achieving high-performance characteristics.
You cannot compromise on the material properties, whether you are using advanced polymers in injection molding or specialized filaments in 3D printing, durability, weight, and functionality can go for a toss if the material isn’t chosen well.
At Cubein we use our expertise to deliver lightweight composites for applications involving automotive, and carefully choose materials that withstand high temperatures for engine components. When you partner with us you get a balanced approach involving material cost with required performance attributes to maximize ROI for our clients.
4. Utilize Simulation Tools for Design Validation
What if you could test your product’s performance in a virtual world before even building it? Wouldn’t it be far smarter and more cost-effective to use simulation software to ensure the product does what it is intended to without spending an exorbitant amount?
Simulation software has changed the way businesses test product performance under real-world conditions. It has reduced the need for physical testing and ensured that the final design is set for success.
The simulation does all that can be done in the real world. It evaluates stresses and deformations to improve durability, ensure components can handle heat without failure, and much more.
No wonder almost 87% of the respondents to a survey by McKinsey affirmed that simulation tools improved product performance and were the top value driver by a significant margin.
5. Design for Scalability
What’s the use of making a one-off average product that is made without the potential of reaching the global markets? High-performance products that are designed with scalability in mind have the potential to transition from prototypes to mass production.
Industry giants like Deloitte have highlighted that 72% of companies prioritize scalable manufacturing design to meet growing demand while maintaining flexibility in product customization.
At Cubein we use injection molding for scaling up the production of quality-assured high-performance products once a validated design is ready and include industry-leading best practices for scalability taking special care to use common parts and materials with special emphasis on designing products that can be easily customized with interchangeable parts.to smoothen manufacturing.
6. Prioritize Quality Control and Precision
At Cubein as the leading industrial design and manufacturing company and turnkey manufacturers, we integrate quality control into each step of the process. This is because, in our experience with industrial products, we have understood that tolerances and precision directly impact performance.
Hence product companies must use quality control techniques that involve dimensional accuracy checks using precision measuring tools to ensure adherence to design specifications.
Additionally, material integrity testing is a key component to ensure the best results, and implementing automated inspection systems for consistent quality is the way forward for sustained results.
Revolutionize Your Product Design with Future-Centric Strategies
Though technology has picked up pace the basics of delivering high-performance quality-led products start at the basics. In this blog, we have included all the strategies that are a must for product companies and OEMs to make it big in global markets.
Designing high-performance industrial products requires a combination of smart strategies, advanced tools, and well-implemented manufacturing processes.
At Cubein as a leading industrial design and manufacturing company, we provide turnkey 3D printing, injection molding, and contract manufacturing services that ensure that the final product is fit to tackle any kind of challenge arising from the market backed by a solid product design strategy. With Cubein you can take your product from concept to final product, and ensure superior quality and reduced time to market.