What’s the Difference Between Selective Laser Sintering (SLS) and Selective Laser Melting (SLM)?
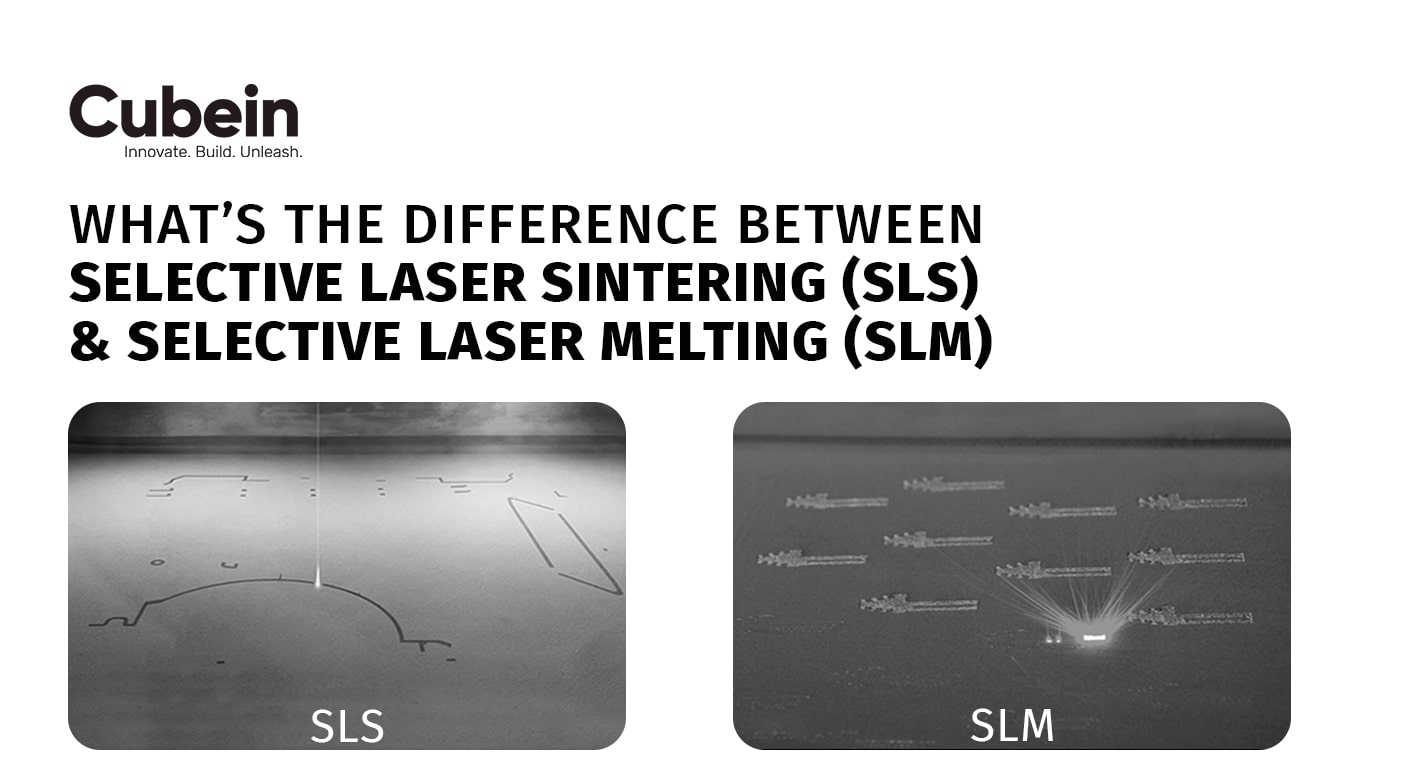
The two of the most widely used techniques in the additive manufacturing industry are Selective Laser Sintering (SLS) and Selective Laser Melting (SLM) . Despite their similarities, these methods have distinct differences that can significantly impact the final product.
Understanding the difference between (SLS) and (SLM) is crucial for anyone involved in 3D printing, as it helps in selecting the appropriate method for specific applications.
Understanding Selective Laser Sintering (SLS)
Selective Laser Sintering (SLS) is an additive manufacturing process that involves the use of a high-powered laser to sinter powdered material, binding it together to create a solid structure. The process starts with a digital 3D model sliced into thin layers by software. The SLS machine spreads a thin layer of powder material over the build platform, and the laser selectively fuses the powder layer by layer according to the design, until the object is fully formed.
Advantages of SLS:
1. Material Versatility: SLS can use a wide range of materials, including polymers, metals, ceramics, and composites.
2. No Support Structures Needed: Unlike other 3D printing methods, SLS utilizes surrounding powder to provide support during the build process, eliminating the need for additional support structures.
3. Complex Geometries: SLS is capable of producing highly complex and intricate geometries that would be difficult or impossible to achieve with traditional manufacturing methods.
Exploring Selective Laser Melting (SLM)
Selective Laser Melting (SLM), on the other hand, is a technique that fully melts the powdered material to create a solid structure. Similar to SLS, SLM begins with a digital 3D model and involves spreading a thin layer of powder material over the build platform. However, the key difference lies in the laser’s intensity and duration. In SLM, the laser fully melts the powder, resulting in a denser and more cohesive final product.
Advantages of SLM:
1. High Density and Strength: Because the material is fully melted, SLM parts tend to have higher density and mechanical strength compared to those produced by SLS.
2. Metals Focus: SLM is predominantly used for metal parts, making it ideal for industries requiring high-strength components, such as aerospace and medical implants.
3. Precision and Detail: SLM can achieve high precision and fine detail, making it suitable for producing intricate parts with tight tolerances.
Key Differences Between SLS and SLM
1. Material State During Process:
– In Selective Laser Sintering (SLS), the powdered material is sintered, meaning it is heated to a point where it fuses together without fully melting.
– In Selective Laser Melting (SLM), the powdered material is completely melted, resulting in a solid and homogenous structure.
2. End-Product Characteristics:
– SLS parts often have a slightly porous structure due to the sintering process, which can affect mechanical properties.
– SLM parts are denser and stronger, with properties comparable to those of conventionally manufactured parts.
3. Applications:
– SLS is versatile and used for a wide range of materials, making it suitable for prototypes, functional parts, and complex geometries.
– SLM is primarily used for high-performance metal parts where strength and precision are critical, such as in the aerospace, automotive, and medical industries.
4. Support Structures:
– SLS does not require additional support structures, as the unsintered powder provides support.
– SLM often requires support structures to prevent warping and ensure stability during the build process, especially for complex geometries.
5. Surface Finish:
– SLS parts may have a rougher surface finish due to the presence of partially fused powder particles.
– SLM parts generally have a smoother surface finish, although post-processing may still be necessary for the best results.
Choosing Between SLS and SLM
When deciding between Selective Laser Sintering (SLS) and Selective Laser Melting (SLM), several factors should be considered:
1. Material Requirements:
– SLS would be a better choice if your project requires a variety of materials, including polymers and composites.
– For high-strength metal parts, SLM is often the preferred method.
2. Mechanical Properties:
– SLM produces parts with superior mechanical properties, making it suitable for load-bearing applications.
– For functional prototypes and parts that do not require the same level of strength,k SLS can be used.
3. Geometric Complexity:
– SLS excels at producing complex geometries without the need for support structures.
– SLM can also produce complex parts but may require additional support, increasing post-processing time.
4. Surface Finish and Detail:
– If a smoother surface finish is critical, SLM might be advantageous due to its fully melted layers.
– SLS parts may need additional finishing processes to achieve the desired surface quality.
5. Cost Considerations:
– SLS can be more cost-effective for certain materials and applications, especially for prototypes and short production runs.
– SLM tends to be more expensive due to the higher energy consumption and need for support removal, but it offers superior material properties.
Understanding the difference between (SLS) and (SLM) is essential for choosing the right additive manufacturing process for your project. While both methods have their strengths, the choice ultimately depends on the specific requirements of the end product.
SLS offers versatility and the ability to produce complex geometries without support structures, making it ideal for prototypes and a variety of materials. SLM, on the other hand, provides superior mechanical properties and precision, making it the go-to method for high-strength metal parts.
By leveraging the unique advantages of each process, manufacturers can optimize their production workflows, reduce costs, and achieve the desired performance characteristics for their applications.
Whether you are developing prototypes, functional parts, or high-performance components, understanding the nuances and difference between (SLS) and (SLM) will help you make informed decisions and stay competitive in the ever-evolving field of additive manufacturing.